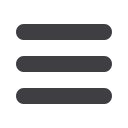
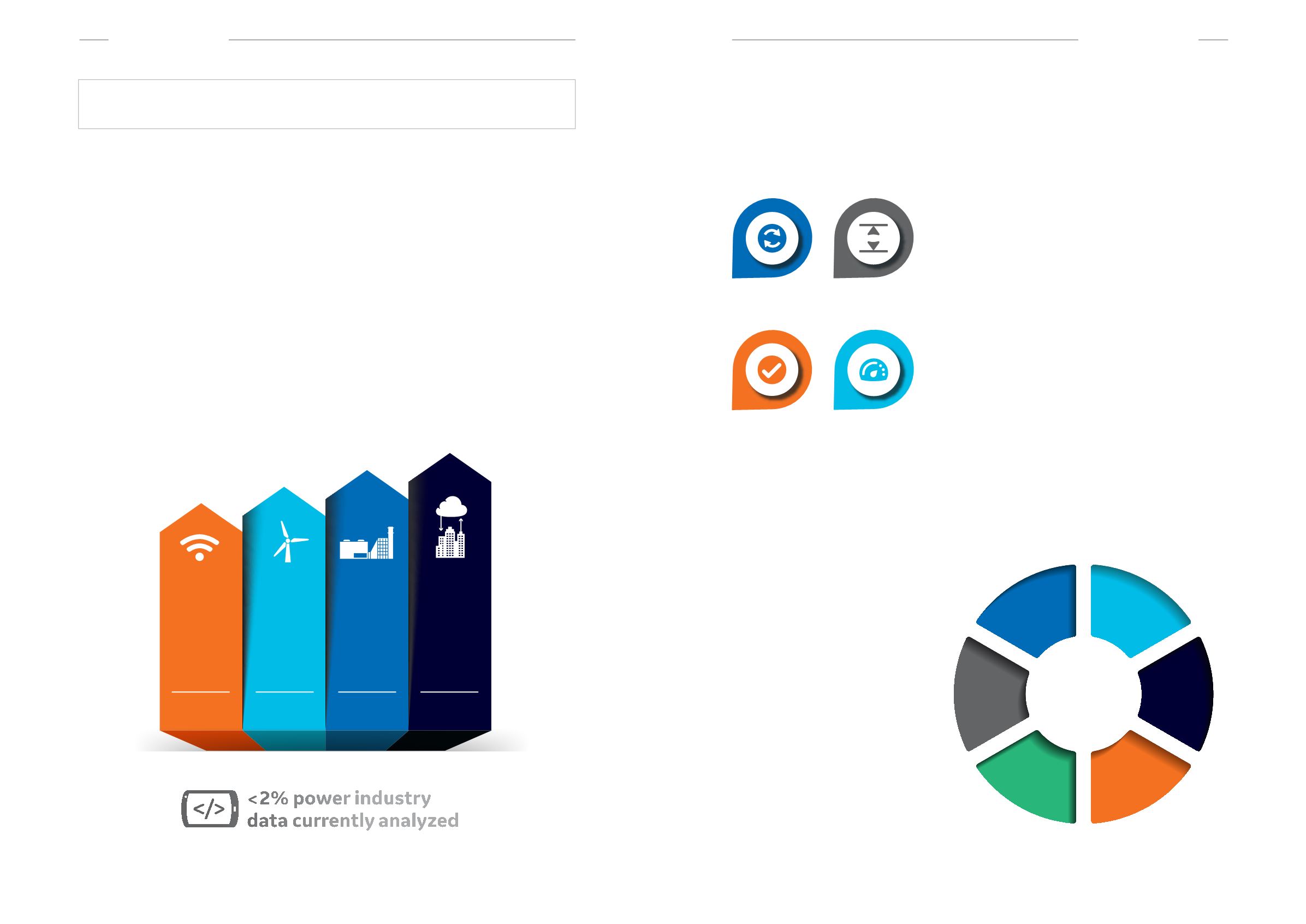
Predix Apps
& Cloud
Interface
Advanced
Control
Apps
Digital
Plant
User Experience
across GT, ST,
BOP
Cyber
Security
Seamless
Controls
Integration
Integrated
Plant
Control
System
FLEXIBILITY
• Startup path options
• Fast load following
CAPACITY
• Boost output
• Manage trades
RELIABILITY
Enhanced grid
services
AVAILABILITY
Performance
recovery odometers
Asset
Monitoring
real time
SMART
DEVICES
UNIT
CONTROLLER
CONTROL
SERVER
CLOUD
Asset
Control
real time
Plant &
Fleet
Optimization
seconds to
minutes
Plant
Control &
Optimization
real and near
real time
GE’s hybrid plant control solution is an integrated plant controller built
on the IICS—a secure, scalable, and distributed control architecture with
a user experience that reduces costs and increases operator efficiency.
The IICS is designed to leverage the power of the Industrial Internet using
GE’s Predix platform that spans from the sensors at the edge to the cloud
to create an ecosystem of connected local plant controls, supervisory
optimization applications, and centralized business applications.
Digital Solutions
Integration Advantage
of an OEM
GE’S INTEGRATED PLANT CONTROLS
SOLUTION IS MORE THAN A
SUPPLY OF CONTROL SYSTEM
HARDWARE AND SOFTWARE.
It includes the OEM and System
Integration value-added engineering
to bring consistency and harmonization
of controls for a common look and
feel and operating experience across
the plant equipment and systems. The
GE Integrated plant control solution
provides benefits to the end user for
operations and maintenance; benefits to
the EPC for engineering time and quality;
while enabling design, installation and
commissioning cycle advantages.
BUILDING BLOCKS
THE HARDWARE AND SOFTWARE THAT FORM THE IICS IN A
HYBRID POWER PLANT IS SOMETIMES REFERRED TO AS THE
“SECRET SAUCE” OF THE SYSTEM. IT ENABLES THE INDIVIDUAL
COMPONENTS IN THE SYSTEM TO OPERATE EFFECTIVELY
TOGETHER AND INTERFACE SEAMLESSLYWITH THE GRID.
THE DIGITAL JOURNEY BEGINSWITH THE
CREATION OF AN INTEGRATED PLANT
SYSTEMMODEL THAT INCORPORATES THE
3D ARRANGEMENTWITH ITS DIGITAL TWIN,
a collection of physics-based methods and advanced
analytics that model the present state of assets in a
virtual view of the power plant.
These system-level models utilize both physics-based
domain knowledge as well as terabytes of operational
and test data to simulate asset-level and plant-level
performance, cost, emissions, and life. GE’s machine-
learning algorithms will evolve the Digital Twin throughout
the plant’s life cycle and build “what if” scenarios to help
improve plant design, construction and operation. Once
constructed, derivatives of this Digital Twin are core to
the software solutions (apps) that control and optimize
operational outcomes such as flexibility, capacity,
efficiency, availability, and emissions.
Industrial Internet Control
System (IICS)
so l ut i ons
so l ut i ons
24 /
HYBRID SOLUTIONS
/
www.gepower.com/hybrid www.gepower.com/hybrid/
HYBRID SOLUTIONS
/ 25